Crafting Proactive Thermal Management Plans for Electrical Enclosures
Excess Heat in Electrical Enclosures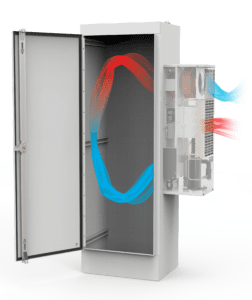
Excess heat in electrical enclosures is a high-stakes problem. These enclosures often contain vital electronics that are not only critical to production, but also expensive. Failing to effectively manage heat buildup can degrade enclosed electronics, leading to costly replacements. It can also shut down systems, leading manufacturers to incur even more costs from unnecessary downtime.
The high stakes of excess heat makes proper cooling crucial for effective and efficient production. Proper cooling requires manufacturers to consider heat load, ambient temperature, particles and debris, enclosure location, material, and other complex factors. Most manufacturers lack effective thermal management plans for electrical enclosures, risking significant financial losses that can easily be prevented with proper cooling.
Developing a Thermal Management Plan with Pfannenberg
Manufacturers looking to reduce costs and improve uptime by developing proactive thermal management plans for enclosures can benefit from Pfannnenberg’s 70 years of expertise. Pfannenberg can help determine if a manufacturer employs the correct cooling solutions for their unique facilities and craft a thermal management plan. The plan activities include verifying that the size of cooling methods meet the thermal loads of enclosures, identifying critical equipment, and recognizing thermal technology that may be underperforming due to poor maintenance putting steps in place to reduce downtime Pfannenberg can also help develop a preventive maintenance plan and recommend the correct thermal technology for challenging applications.
Executing a Thermal Management Plan with Pfannenberg Solutions
Pfannenberg offers thermal management solutions for diverse manufacturing environments. These solutions can be a critical component of a thermal management plan by delivering high performance and precision.
The PKS 3000 Series Air/Air Heat Exchangers use Pfannenberg’s Kinetic Cooling System™ to remove heat from electrical enclosures using ambient air. These exchangers suit environments with cooler ambient air or dirty air. They offer reduced maintenance and robust performance across indoor, outdoor, remote, and washdown applications that demand a closed-loop system for electronics protection.
Pfannenberg’s Air/Water Heat Exchangers serves environments with high ambient temperatures or washdown areas with significant particulates. Designed for both internal and external installation, these exchangers are maintenance-free and energy-efficient, using a supplied water source to achieve cooling capacities ranging from 2,218 BTU to 34,121 BTU. This ensures safe and efficient cooling of enclosure electronics, making these exchangers ideal for a wide range of industrial applications.
Pfannenberg Cooling Units provide a closed-loop system that seals out ambient air and recirculates clean, cool air into the enclosure, which prevents overheating and critical temperature fluctuations. These units help maintain internal temperature at or below ambient levels, and also provide higher ingress protection when surrounding air is contaminated with oil or conductive dust.
For less demanding environments, Pfannenberg’s Filterfans® offer a cost-effective thermal management solution. With tool-free installation, superior airflow, and extended filter lifespan, Filterfans® provide Type 12 or Type 3R protection. This makes Filterfans® particularly suitable for clean, non-hazardous environments where ambient temperature outside the enclosure is lower than internal temperature.
Proactive Plan + High-Performance Products: An Ideal Thermal Management Solution
In fast-paced manufacturing environments, crafting a proactive thermal management plan for electrical enclosures keeps operations running smoothly and avoids costly downtime. Pfannenberg’s experience and market-leading solutions provide manufacturers with tools they need to protect their vital electronics and optimize efficiency. By partnering with Pfannenberg, manufacturers ensure they have the right cooling systems in place, improving performance, reducing costs, and increasing reliability. Taking proactive steps in thermal management with Pfannennberg helps secure more efficient and dependable operations for years to come.
Learn more here about our service and maintenance options here.